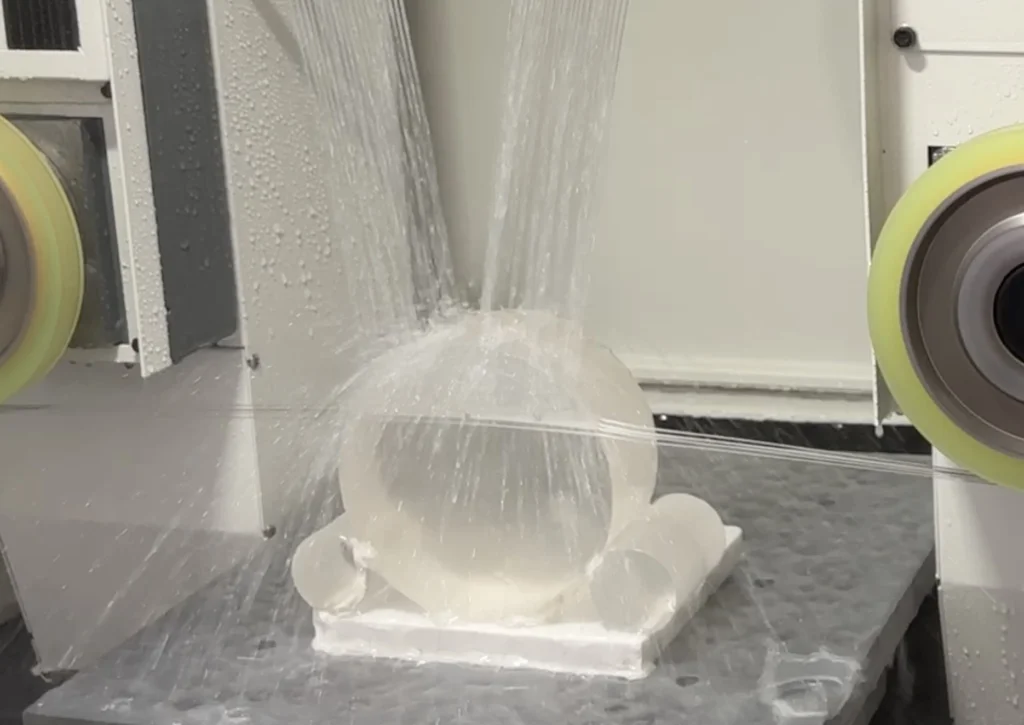
Sapphire, known for its exceptional hardness and optical transparency, has become a crucial material in various high-tech industries, from optoelectronics to advanced optical components. Precision Sapphire Cutting, however, presents unique challenges due to its extreme hardness (Mohs 9, second only to diamond) and brittleness. This article explores the intricacies of sapphire cutting and details our recent cutting experiment, highlighting the capabilities of our endless diamond wire saw in processing this challenging material.
Challenges in Sapphire Cutting
Sapphire’s hardness makes it an excellent choice for demanding applications, such as optical windows, laser components, and electronic substrates. However, these same properties make cutting sapphire a difficult and time-consuming process. Traditional cutting methods often struggle with the hardness of sapphire, resulting in increased material waste, surface damage, and micro-cracking. To overcome these challenges, precision cutting tools like diamond wire saws are essential.
One of the primary difficulties in sapphire cutting is managing the balance between cutting speed and surface quality. Cutting too quickly can generate excessive heat, which leads to thermal stress and potential cracking. On the other hand, cutting too slowly, while producing a better-quality finish, may not be feasible for commercial-scale production due to increased time and costs. This makes choosing the right cutting technique and parameters a critical factor in achieving efficiency while maintaining quality.
Traditional Sapphire Cutting Methods
Traditional methods for cutting sapphire include diamond blade circular saws and conventional diamond wire saws. Each method has its limitations when dealing with sapphire’s extreme hardness and brittleness:
- Diamond Blade Circular Saws: These saws use a rotating diamond-coated blade to cut through the sapphire. While effective for rough cutting, the high friction generated often leads to significant heat buildup, which can cause thermal stress and increase the risk of micro-cracking. Additionally, the surface quality is generally inferior, requiring further polishing steps.
- Conventional Diamond Wire Saws: Conventional diamond wire saws use a long diamond-coated wire that moves back and forth to cut through the material. The reversing motion can leave visible wire marks on the surface, leading to the need for additional finishing. Furthermore, the back-and-forth motion limits the cutting speed, making the process more time-consuming compared to modern techniques.
Endless Diamond Wire Saw: A Game Changer
Our endless diamond wire saw is specifically designed to tackle such challenges by utilizing a looped diamond wire that continuously moves in one direction, ensuring a smooth and even cut. Unlike traditional diamond wires that need to reverse direction, the endless wire maintains a consistent cutting speed, reducing the occurrence of visible wire marks and enhancing surface quality.
To demonstrate its capability, we recently conducted a cutting experiment on a 50 mm diameter sapphire rod. The goal was to slice the rod into 5.3 mm thick wafers while maintaining precision and minimizing material loss.
Experiment Overview: Sapphire Cutting Results
- Material: 50 mm diameter sapphire rod
- Target: 5.3 mm thick wafers
- Cutting Time: Approximately 30 minutes per slice
- Cutting Speed: Our endless diamond wire operated at a speed of 35 m/s linear speed to balance between precision and efficiency. The feed rate was set at 2 mm/min.
- The machine model we use: SGR-40
The experiment was successful in achieving the desired results. The cutting surface was exceptionally smooth, with no visible wire marks, and the dimensional accuracy of the wafers was well within acceptable tolerances. Compared to traditional methods, the endless diamond wire saw provided a significant advantage in terms of both efficiency and surface quality. This result is particularly important for industries like optoelectronics, where even the slightest surface imperfections can affect the performance of components.
Applications of Sapphire Wafers
The 5.3 mm thick sapphire wafers produced are ideal for a range of applications:
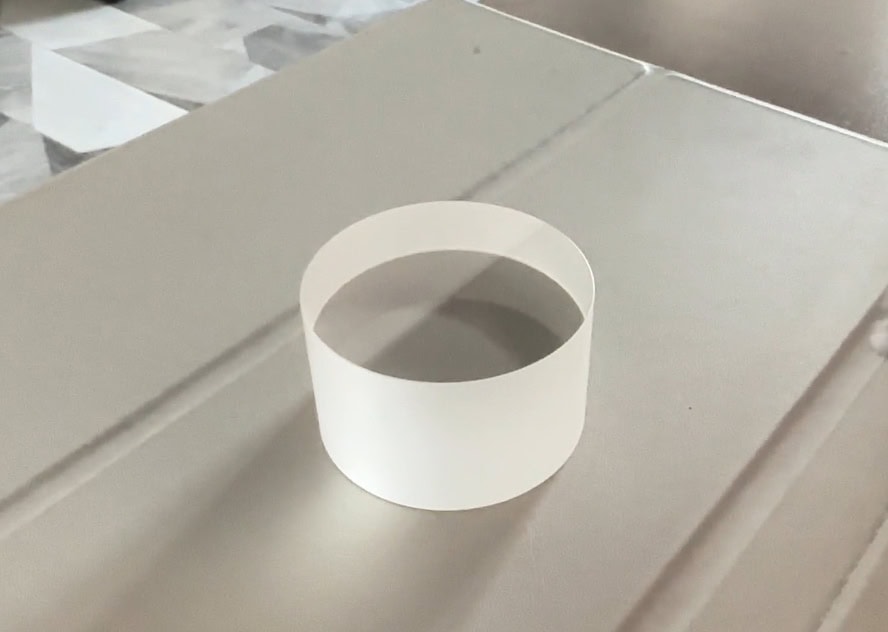
- Optical Windows: Due to their excellent optical clarity and thermal resistance, sapphire wafers are commonly used in high-temperature viewports and laser windows.
- Semiconductor Substrates: Sapphire is often used in the semiconductor industry for Silicon on Sapphire (SOS) technology, which improves the performance of RF devices.
- Optoelectronics: Sapphire’s transparency across UV to IR wavelengths makes it valuable for LEDs and other optoelectronic components.
Conclusion
Cutting sapphire is challenging, but with the right technology, it is possible to achieve high-quality results efficiently. Our recent cutting experiment using the endless diamond wire saw illustrates how advances in cutting technology can meet the demands of even the toughest materials. By maintaining a controlled cutting speed and optimizing the feed rate, we were able to achieve precision cuts with minimal waste, contributing to improved efficiency in production and enhanced product quality.
As industries increasingly demand high-performance materials like sapphire, innovations in cutting technologies will continue to play a crucial role in enabling these advancements. Our endless diamond wire saw stands at the forefront of these innovations, delivering reliable, high-precision cutting solutions for even the hardest materials.