Introduction: The Push for Cleaner, Smarter Cutting
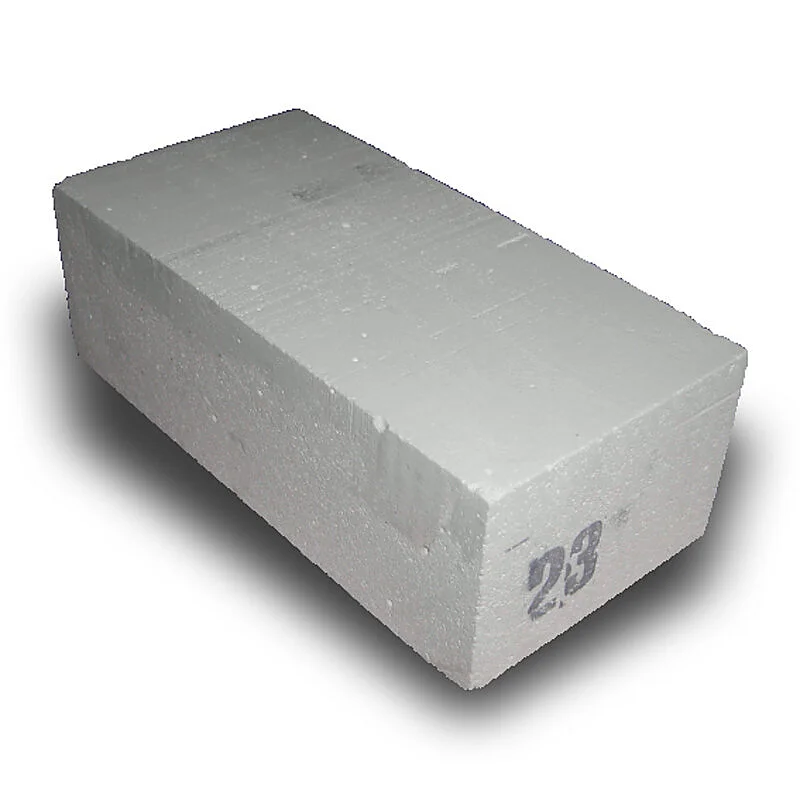
As energy-saving construction materials like PU insulation bricks become mainstream, manufacturers face a new challenge—how to make Insulation Brick Cutting efficiently, cleanly, and with precision. Traditional cutting methods often generate dust, deformation, or edge melting, which doesn’t align with the quality standards of modern green building products.
This is why Máy cắt dây kim cương are now becoming the preferred tool for insulation brick cutting—not only because of their accuracy, but because of the clean process and long-term cost advantages.
The Challenges of Cutting Insulation Bricks
Polyurethane foam has a unique profile:
- Soft core, easy to compress
- Sensitive to heat—melts under friction
- Requires consistent thickness and flat surfaces to function properly in wall systems or panels
Old cutting methods fall short:
- Hot wires burn the foam and emit fumes
- Band saws produce dust and edge chipping
- Rotary blades deform thick blocks under pressure
Each of these issues leads to poor fit, material waste, or extra finishing work—all of which reduce profitability and slow down production.
How Diamond Wire Saws Solve the Problem
Các cưa dây kim cương vô tận approaches insulation brick cutting differently. Instead of slicing, it gently grinds through the material using a tensioned abrasive loop. The results are consistent across hundreds of cuts.
🔹 Smooth and Square Cut Surfaces
The grinding action leaves no edge melt, no blade marks, and no compression distortion.
🔹 Stable Wire Path = Stable Tolerance
CNC control ensures that every PU panel or block comes out with the same dimension and thickness, panel after panel.
🔹 No Heat, No Dust Cloud
The process is dry, clean, and cool—no VOCs, no sticky residue, no dusty cleanup.
🔹 Designed for Long-Term Operation
With fewer moving parts and low wear, wire saws require less maintenance than blades or hot wire frames.
Cost and Efficiency Gains
Manufacturers who switch to diamond wire for insulation brick cutting often report:
- 30–50% less scrap from rejected cuts
- Better foil lamination adhesion due to clean surfaces
- Fewer filter replacements in air handling systems
- Higher production uptime, especially on large-format panels
Real-World Example: A Thermal Panel Producer’s Upgrade
One mid-size panel producer in the Middle East had been using hot wire systems for cutting PU bricks. They struggled with inconsistent panel fit and visible edge damage. After switching to an endless diamond wire saw, they reported:
- Cut accuracy within ±0.2 mm across 1.2-meter blocks
- No further complaints from the laminating line
- Easier compliance with ISO 9001 and green building material certifications
In their words:
“We didn’t realize how much performance we were losing until we upgraded the cutter.”
Conclusion: Future-Proof Your Insulation Brick Cutting Process
When your end customers demand high thermal efficiency, you need more than just a foam block—you need perfectly cut, clean, uniform insulation bricks. That’s what diamond wire saws deliver.
If insulation brick cutting is part of your production line, it’s time to rethink your cutting strategy.
📩 Reach out to our technical team and explore how a diamond wire system could work for your application.